Author
katherinejunda
Share
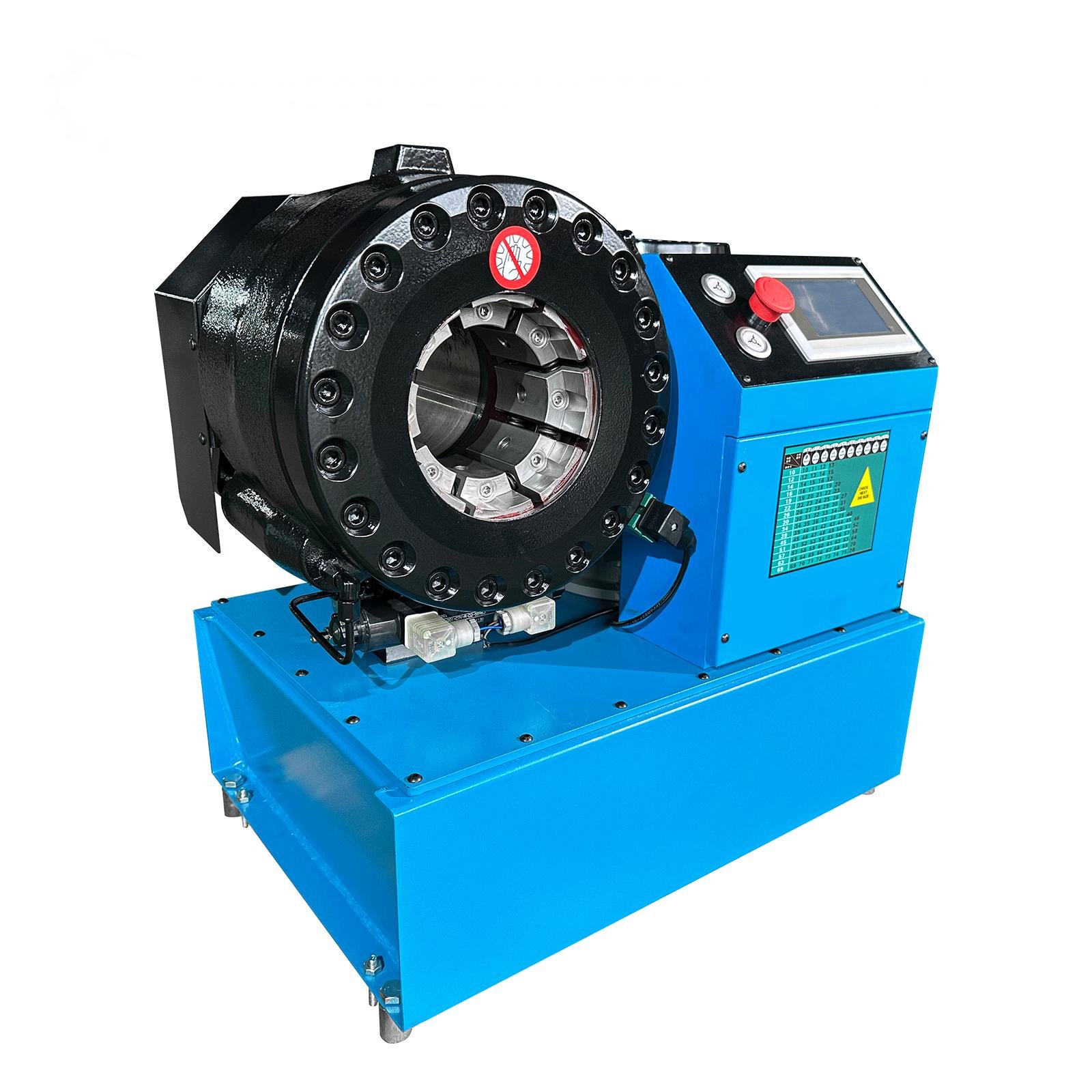
Hose crimping machine advantages in production
Hose crimping machines provide numerous advantages in production environments, particularly for high-volume operations. Here’s a look at how they benefit production lines:
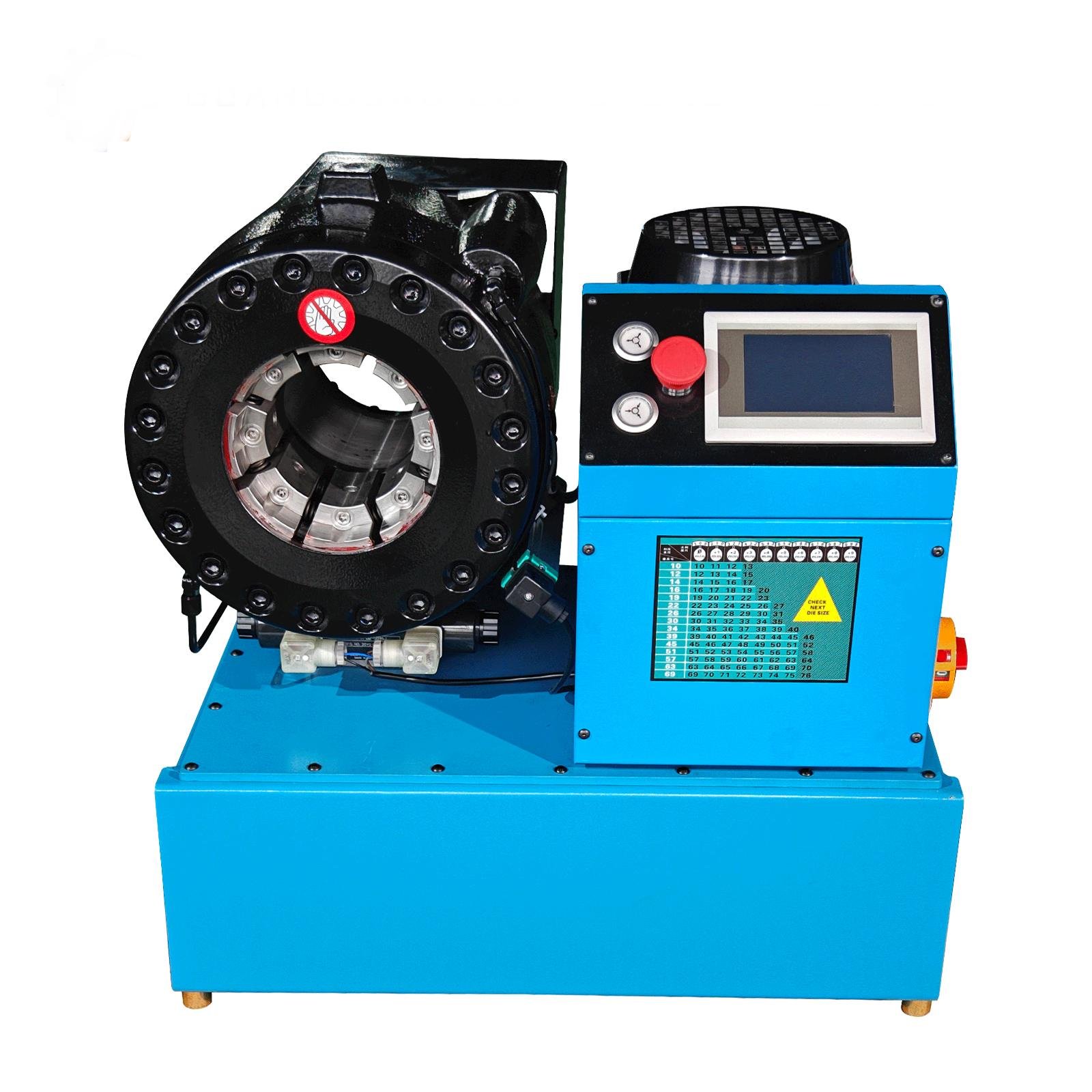
GT-10
1. High Efficiency and Speed
- Hose crimping machines automate the crimping process, significantly increasing the speed at which hoses can be produced. They are ideal for high-volume production, enabling faster cycle times and supporting tight production schedules.
2. Consistent Quality and Precision
- These machines deliver precise and uniform crimps every time, ensuring high-quality, reliable connections. Consistency is crucial in production settings, as it minimizes the risk of leaks or failure in finished products, which could otherwise lead to costly reworks or customer dissatisfaction.
3. Reduced Labor Costs
- Automated crimping machines reduce the need for manual labor, freeing operators to focus on other tasks. This not only cuts down labor costs but also improves productivity as fewer skilled technicians are needed to achieve high-quality crimps.
4. Increased Production Capacity
- By speeding up the crimping process and reducing downtime, hose crimping machines can help increase the overall production capacity. This allows manufacturers to meet higher demand without sacrificing quality or increasing lead times.
5. Lower Scrap and Material Waste
- Consistent crimp quality reduces the chance of errors that lead to rejected parts or waste. Automated settings and precise controls prevent under or over-crimping, minimizing scrap rates and maximizing the use of materials.
6. Enhanced Safety for Operators
- Modern hose crimping machines come with built-in safety features, such as automatic shut-offs, pressure relief systems, and emergency stop buttons. These features help protect operators, making the production floor safer and reducing the likelihood of injuries.
7. Ease of Use and Training
- With intuitive interfaces and programmable settings, hose crimping machines are easy to operate, even for less experienced staff. Many models include touchscreens and pre-set crimping parameters for different hose types, making training simpler and faster.
8. Integration with Production Systems
- Many advanced crimping machines can connect to factory automation systems, allowing for data collection, performance monitoring, and integration with quality control systems. This connectivity helps streamline production management and ensures traceability for quality assurance.
9. Flexibility for Various Hose Types and Sizes
- Production facilities often need to crimp hoses of different types and sizes. Modern crimping machines are versatile, with easily interchangeable dies and settings, enabling quick adaptation to different product requirements without significant downtime.
10. Long-Term Cost Savings
- While hose crimping machines can require a higher initial investment, their durability, reliability, and efficiency provide long-term cost benefits. Reduced downtime, consistent quality, and lower labor costs result in a favorable return on investment (ROI) over time.
In summary, hose crimping machines enhance production efficiency, quality, and safety, providing a competitive advantage in industries that require high output and stringent quality standards.
Table Of Content